Клапані пружини
Для належної перевірки стан клапанних пружин необхідний спеціальний тестер пружин. Якщо його немає у вашому розпорядженні, то можна провести просте порівняння старої та нової клапанних пружин. З цією метою взяти стару та нову клапанні пружини та затиснути їх у лещата. Повільно стискаючи губки лещат, спостерігати за ступенем стиснення обох пружин. Якщо вони стискаються однаково, це свідчить про хороший стан старої пружини. Але якщо у пружини, що працювала, великий ступінь стиснення (виглядає коротше за нову), то це явна ознака втомного зносу - таку пружину слід замінити. Пружини клапанів замінюють на повний комплект.
Підготовлені до встановлення пружини виставляють на рівній та гладкій поверхні (на склі) таким чином, щоб щільно зімкнуті витки знаходилися знизу. Зверху на пружини кладеться металевий куточок та перевіряється зазор між верхнім витком пружини та площиною куточка. Цей проміжок не повинен перевищувати 2,0 мм. В іншому випадку пружини підлягають заміні.
Напрямні втулки клапанів
Напрямні втулки клапанів, виконані з чавуну, мають різні діаметри для впускних та випускних клапанів. Напрямні втулки випускних клапанів мають більший внутрішній діаметр і коротше, завдяки чому їх легко розсортувати. Простягаючи через втулки змочену в бензині ганчір'я, проведіть чистку втулок. Стрижні клапанів найкраще чистити металевою щіткою, що обертається, закріпленою в електродриль.
Контроль зношування напрямних втулок проводиться за допомогою каліброваної оправки. Якщо вибракування калібр оправки вільно входить у напрямну втулку, то таку втулку слід замінити новою. Для демонтажу втулок слід скористатися спеціальною оправкою зі уступом. Якщо є можливість використання направляючих втулок 1-го стандартного розміру, то для їх монтажу використовують спеціальну оправку, за допомогою якої направляючу втулку запресовують посадкове гніздо до тих пір, поки стопорне кільце не увійде в паз на головці блоку циліндрів. При встановленні напрямних втулок ремонтних розмірних груп посадочні гнізда необхідно попередньо обробити протяжними ручними розгортками. Оскільки напрямні втулки перед запресовуванням повинні охолоджуватися сухим льодом, рекомендуємо передати головку блоку циліндрів на СТО для встановлення нових напрямних втулок.
Перед заміною направляючих клапанів клапанів спочатку перевіряють загальний стан головки блоку циліндрів. Після запресування втулки розточують до необхідних розмірів: 8,00-8,015 мм для впускних клапанів та 9,00-9,015 для випускних клапанів. Напрямні втулки випускних клапанів мають більшу довжину.
При заміні напрямних втулок необхідно замінити клапани, а клапанні сідла - прошліфувати.
Примітка. Шліфування клапанних сідел проводиться тільки після заміни напрямних втулок клапанів. Якщо раптом з'ясується, що сідла більше неможливо розточувати, то напрямні втулки не слід змінювати.
Клапанні сідла
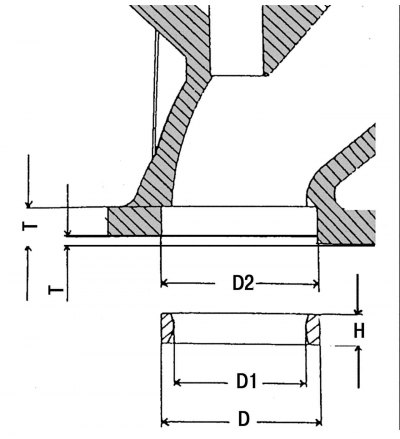
Мал. 37. Основні розміри сідел клапанів: D - Зовнішній діаметр сідла клапана; D1 - внутрішній діаметр сідла клапана; D2 - посадкове гніздо під клапанне сідло в головці блоку циліндрів; Н - висота клапанного сідла; Т - відстань між площиною головки блоку циліндрів та верхньою кромкою клапанного сідла; Н = 6,97-7,00 мм - для всіх клапанів; Т = 2,37-2,25 мм - для впускних клапанів; Т = 2,44-2,25 мм - для випускних клапанів
Якщо підшипники розподільного валу сильно зношені, то в цьому випадку немає необхідності розточувати клапанні сідла, а замінити головку блоку циліндрів у зборі. Сідла клапанів перевіряються на зношування або утворення раковин. Сліди невеликого зношування можна усунути фрезеруванням за допомогою 45-градусної конічної фрези. Якщо клапанне сідло через велику виробку стало дуже широким, то такі сідла підлягають заміні. Клапанні сідла запресовують в головку блоку циліндрів, і знімати їх краще всього шляхом висвердлювання або викручування за допомогою спеціальних розточок. При цьому слід бути дуже обережним, щоб не зашкодити головці блоку циліндрів. Виміряти діаметр базового отвору D1 (Мал. 37) та у разі потреби розточити до наступного ремонтного розміру. Клапанні сідла з ремонтними припусками можуть розточуватися доти, доки не забезпечуватиметься запропоноване перекриття 0,068–0,10 мм. Сідла впускних клапанів мають більший діаметр.
Головку блоку циліндрів нагріти на водяній бані до 90°С, а клапанне сідло остудити на сухому льоду, після чого його можна буде запресувати спеціальною оправкою в гніздо. Цю операцію рекомендується проводити на СТО.
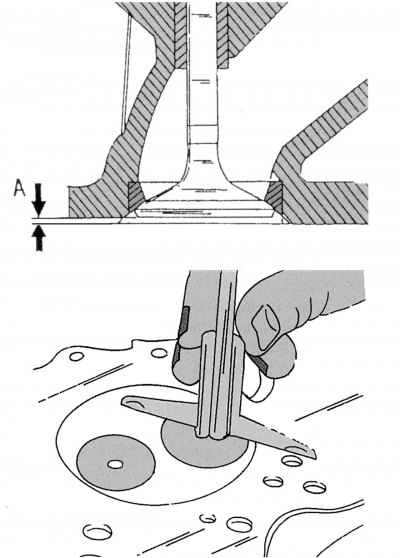
Мал. 38. Визначення розміру А
Обробити клапанне сідло відповідним зенкером та шліфувальним кругом на клапанній шліфувальній машинці. З використанням клапана виміряти максимальну відстань А, як показано на нижній частині рис. 38. При встановленні нових клапана та клапанного сідла відстань А повинна становити 0,1–0,5 мм. Межа зносу становить 1,0 мм.
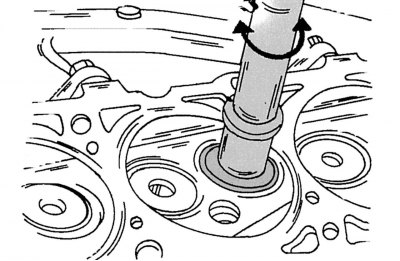
Мал. 39. Притирання клапанів до сідл
Після обробки виміряйте ширину пояса ущільнювача клапанного сідла. Якщо ширина пояса ущільнювача сідла впускного клапана відрізняється від значення 2,5 мм, а сідла випускного клапана - від значення 3,5 мм, то такі сідла необхідно обробити 15-градусною фрезою у верхній частині і 60-градусною фрезою в нижній частині. Фрезерування припиняється, як тільки ширина пояса ущільнювача клапанного сідла входить у зазначені вище межі. Після фрезерування необхідно виконати притирання клапанних сідел. Для цього на сідло клапана наноситься невелика кількість шліфувальної пасти. Зверху на головку клапана кріпиться присоска, за допомогою якої клапану повідомляються обертальні рухи то в один, то в інший бік (Мал. 39). Іноді потрібно повертати клапан на чверть оберту, а потім знову притирати обертальними рухами. За потреби треба додати шліфувальну пасту на сідло клапана. Після притирання видалити залишки пасти з клапана та сідла та проконтролювати посадку клапана на сідлі та головці. На обох частинах повинен чітко проглядатися матовий поясок, що утворився, який і визначає ширину ущільнюючого пояса клапанного сідла.
Олівцем нанесіть кілька рисочок на матовому пояску, що вийшов, з інтервалом 1 мм по його периметру. Після цього опустити клапан у сідло і провернути його на 90°навколо стрижня, злегка притискаючи клапан до сідла.
Вийміть клапан із сідла та перевірте, щоб зникли мітки олівця. Якщо ширина ущільнювальних поясів клапанних сідел знаходиться в межах, то головку блоку циліндрів можна встановлювати на двигун. В іншому випадку необхідно продовжувати обробку та притирання сідел або замінити головку блоку циліндрів.
Клапани
Внаслідок використання гідравлічних компенсаторів зазору в клапанах кінці клапанних стрижнів впускних і випускних клапанів піддаються спеціальної обробки для того, щоб витримувати підвищені навантаження. Незначні пошкодження на головках клапанів можна усунути шляхом їх притирання до сідл, як було описано вище. Більш серйозні пошкодження поверхонь ущільнювачів можна виправити на клапанному шліфувальному верстаті. На відшліфованих клапанах товщина кромок їх тарілок не повинна бути менше 0,5-0,7 мм для впускних клапанів і 0,5-0,6 мм для випускних.
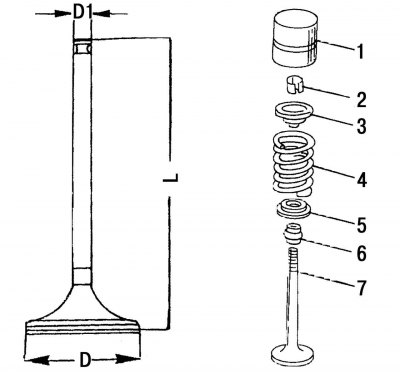
Мал. 40. Основні розміри клапанів: D - діаметр тарілки (головки) клапана; D1 - діаметр стрижня клапана; L - Довжина клапана; 1 - штовхач; 2 - конічні сухарі; 3 - тарілка клапанної пружини; 4 - клапанна пружина; 5 - нижня опорна тарілка клапанної пружини; 6 - масловідбивальний ковпачок; 7 - клапан
На цих типах двигунів використовуються клапани без заповнення натрію, як це мало місце на інших типах двигунів фірми Mercedes-Benz. На рис. 40 наведено розміри клапанів. Клапани, розміри яких не відповідають зазначеним розмірам, мають бути замінені на нові.
При оформленні замовлення на клапани необхідно завжди вказувати їх призначення (впускні чи випускні), а також те, що ці клапани призначені для дизельного двигуна.
У деяких випадках можна замінити лише випускні клапани, якщо вони, наприклад, прогоріли кромки.
Головка блоку циліндрів
Ретельно почистити привалювальні поверхні головки блоку циліндрів та блоку циліндрів, а потім перевірити головку блоку циліндрів на відсутність деформації. З цією метою на привалочну поверхню головки блоку циліндрів помістити лінійку і за допомогою щупа заміряти зазор під лінійкою в поздовжньому, поперечному та діагональному напрямках. Якщо в процесі виміру зазор між лінійкою і поверхнею головки блоку циліндрів у поздовжньому напрямку перевищить 0,10 мм, то головку блоку циліндрів слід направити на спеціалізовану СТО. При встановленні лінійки у поперечному напрямку головки блоку циліндрів під лінійкою не повинно бути жодного просвіту. Головки блоку циліндрів можна шліфувати доти, доки відповідне коригування висоти клапанів дозволить це робити (розмір А на рис. 38).
Так само необхідно перевіряти висоту виступаючої частини форкамер для впорскування дизельного палива (601-й двигун). Край форкамер повинен виступати на 7,6-8,1 мм.
На СТО передбачений розмір виступаючої частини форкамер може бути виставлений за допомогою набору прокладок ущільнювачів різної товщини, що встановлюються під форкамери. Ця робота повинна обов'язково виконуватися на СТО, тому що для цього необхідний спеціальний інструмент для випресування та запресування форкамер.
Розподільний вал
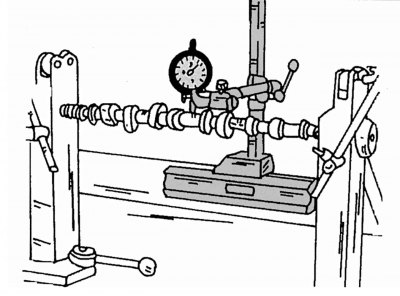
Мал. 41. Перевірка деформації розподільчого валу
Нижченаведений текст описує роботи, пов'язані з перевіркою та контролем стану розподільчого валу. Конструктивний опис розподільчого валу див. 2.12.6. Розподільний вал встановити на призми, що підставлені під крайні опорні шийки, або затиснути між центрами токарного верстата, як показано на рис. 41 а до середньої опорної шийки підвести щуп вимірювального індикатора. Потім, повільно провертаючи розподільний вал, слід стежити показаннями стрілки. Якщо стрілка відхилиться за розподіл 0,01 мм, це означатиме, що вал деформований і підлягає заміні.
Заміна масловідбивних ковпачків (головка блоку циліндрів встановлена на двигуні)
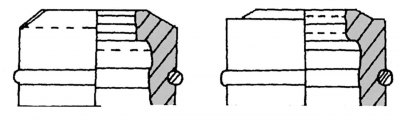
Мал. 42. Форма масловідбивних ковпачків, що одягаються на стрижні клапанів: ліворуч - для випускних; праворуч - для впускних клапанів
Масловідбивні ковпачки можна знайти в ремонтному комплекті. До складу ремонтного комплекту входять захисні втулки, які при монтажі надягають на стрижні впускних клапанів. Масловідбивні ковпачки для впускних та випускних клапанів відрізняються один від одного як своїми діаметрами, так і формою, тому переплутати їх неможливо (Мал. 42).
Для встановлення ковпачків зазвичай використовується спеціальний інструмент. Якщо його немає під рукою, то можна скористатися тонкою трубкою, але дуже обережно, щоб не пошкодити манжети ущільнювачів і стяжні пружинки ковпачків. При встановленні масловідбивних ковпачків на стрижні клапанів, у останніх повинні бути зняті сухарі та клапанні пружини. Для виключення падіння клапана в циліндр необхідно, щоб поршень цього циліндра знаходився у ВМТ. На чотирициліндрових двигунах ця операція істотно полегшується завдяки тому, що щоразу два поршні знаходяться у ВМТ. На п'ятициліндрових двигунах виконувати цю роботу трохи складніше, оскільки щоразу необхідно провертати колінчастий вал двигуна на певний кут, встановлюючи поршень чергового циліндра у ВМТ. Заміну масловідбивних ковпачків необхідно виконувати наступним чином (рекомендуємо доручити виконати цю роботу досвідченому фахівцю).
Прокрутити двигун до встановлення поршня першого циліндра у ВМТ.
Демонтувати розподільний вал (підрозд. 2.12.6).
Видалити сухарі клапанів першого циліндра, як описано в підрозд. 2.4.2. На чотирициліндровому двигуні можна одночасно видалити сухарі та зняти клапанні пружини з клапанів четвертого циліндра.
Акуратно, щоб не пошкодити при цьому стрижні клапанів і отвори штовхачів, зірвати щипцями старі ковпачки.
Нові олійні ковпачки змастити маслом і акуратно проштовхнути вниз по стрижням клапанів. Не забувайте надягати на стрижні впускних клапанів захисні втулки. Щільно насадити масловідбивні ковпачки на напрямні втулки клапанів.
Встановити клапанні пружини кольоровим маркуванням вниз і встановити сухарі клапана, стежачи за тим, щоб сухарі добре сіли в пази та конічні поглиблення верхніх опорних тарілок клапанних пружин.
Злегка підняти зірочку приводу розподільного валу для того, щоб ланцюг не вийшов із зачеплення, і провернути колінчастий вал чотирициліндрового двигуна на півоберта. Після цього можна аналогічним чином поміняти масловідбивні ковпачки на клапанах другого та третього циліндрів. При роботі на п'ятициліндровому двигуні колінчастий вал необхідно повертати доти, поки поршень наступного циліндра не досягне ВМТ. Чергування наступних циліндрів, поршень яких проходить ВМТ: 2-4-5-3. Як зазначалося вище, проведення цієї роботи потребує особливої ретельності.
Примітка. Пристрій для стиснення клапанних пружин слід затискати дуже повільно, оскільки сухарі деяких клапанів зависають у пазах. Уникайте ситуацій, коли внаслідок швидкого затискання пристрою клапан упирається своєю тарілкою в поршень. Пристрій повинен впливати лише на клапанну пружину, стискаючи та переміщуючи її вниз.