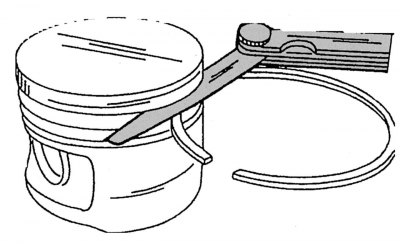
Мал. 58. Вимірювання вертикальних зазорів у канавках поршневих кілець за допомогою щупа
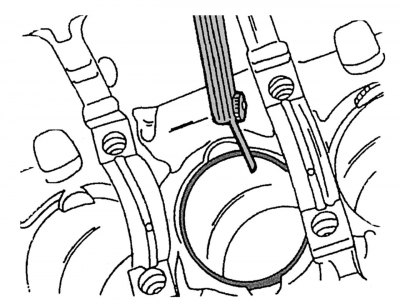
Мал. 59. Вимірювання зазорів у замках поршневих кілець, що знаходяться в циліндрах двигуна
Провести ретельний контроль усіх деталей. За наявності задир, подряпин і слідів зносу замінити їх новими. Виміряти вертикальний зазор у канавках поршневих кілець за допомогою щупа, що вставляється між площиною поршневого кільця і площиною канавки поршневого кільця, як показано на рис. 58 (канавки необхідно перед цим ретельно прочистити, для цього можна, наприклад, використовувати зламане поршневе кільце). Якщо результати вимірів покажуть, що зазори у верхніх кільцях перевищують 0,20 мм, в середніх - 0,15 мм і в маслознімних - 0,10 мм, це свідчить про знос поршневих кілець або поршнів. Потім з внутрішньої сторони картера двигуна необхідно по черзі вставити поршневі кільця в отвори циліндрів, а перевернутим поршнем зверху посунути вниз так, щоб вони розташувалися горизонтально і знаходилися на відстані 20 мм від нижньої кромки гільз циліндрів. Після цього щупом виміряти зазори в замках поршневих кілець, як показано на рис. 59. На всіх кільцях цей проміжок становить 0,20-0,40 мм. Гранично допустиме зношування для замків верхніх кілець не повинно перевищувати 1,5 мм, для інших кілець — 1,0 мм.
Перевірити поршневі пальці та шатунні втулки на зношування та наявність задирок. У цьому випадку допускається одиночна заміна несправного шатуна, проте маса нового шатуна не повинна відрізнятися від маси шатуна, що замінюється, більш ніж на 5 г. Заміну втулок у верхніх головках шатунів рекомендуємо проводити на спеціалізованих СТО.
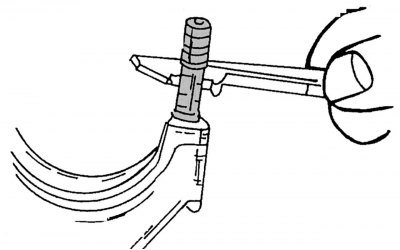
Мал. 60. Вимірювання діаметрів податливої частини болтів кріплення кришок шатунних підшипників
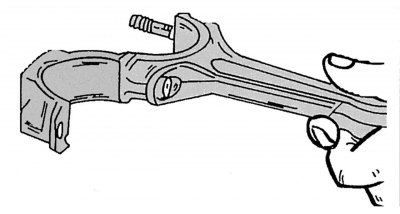
Мал. 61. Контроль шатуна на легкість ходу
Перед повторним використанням болтів кріплення кришок шатунних підшипників необхідно заміряти діаметри їх тонких частин за допомогою штангенциркуля (Мал. 60). Якщо вимірювані діаметри болтів виявляться менше 7,1 мм, то такі болти підлягають заміні, яку слід проводити згідно з наведеними нижче інструкціями. Перед заміною болтів слід виконати ще одну перевірку, яка полягає в наступному: кришка шатунного підшипника садиться на один болт і повертається убік так, щоб шатун і повернена убік кришка підшипника знаходилися на горизонтальній осі, як показано на рис. 61. Якщо кришка підшипника під власною вагою падає вниз, цей шатун повинен бути замінений на новий. В іншому випадку необхідно замінити болти. У пристрої для перевірки шатунів слід перевірити всі шатуни на скручування і вигин, величини яких не повинні перевищувати мінімально допустимі. Для виконання цієї роботи також рекомендується звернутися до спеціалізованої СТО. Під час перевірки поршнів і шатунів існують такі рекомендації.
Не рекомендується повторно використовувати шатуни, які були одного разу перегріті через несправність підшипника (шатуни з кольором втечі).
Шатуни та кришки шатунних підшипників підібрані один до одного та промарковані.
Нові шатуни поставляються із розточеними втулками у верхніх головках, їх можна відразу встановлювати на двигун.
Встановити на болти кришки шатунних підшипників із вкладишами та за допомогою нутроміра проміряти внутрішній діаметр підшипників. Якщо отриманий результат перевищить значення 51619 мм або буде виявлена деяка конусність, то опорну поверхню кришки шатунного підшипника можна скоригувати на рівній плиті до 002 мм.
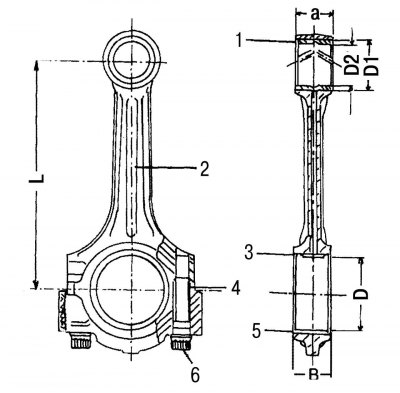
Мал. 62. Шатун: 1 - втулка верхньої головки шатуна; 2 - шатун; 3 - верхній вкладиш підшипника; 4 - пружні затискні штифти; 5 - нижній вкладиш підшипника; 6 - болт кришки шатунного підшипника; L=145 мм; B=24,0 мм; D=47,95 мм; D1 = 29,50 мм; D2=26,0 мм (допуск 0,018-0,024 мм)
Якщо шатун знаходиться в ідеальному стані, а в поршневому пальці виявлено підвищений зазор, необхідно замінити втулку у верхній головці шатуна, випресувавши стару і запресувавши нову. При цьому необхідно звернути особливу увагу на розташування отвору мастила у втулці. Воно має бути на одній лінії зі стрілкою, позначеною на рис. 62. Після запресування нової втулки у верхню головку шатуна її необхідно розвернути до діаметра D2, вказаного на рис. 62. На цьому малюнку вказано допустимий діаметр.