- Wipe the seats of the main bearings of the crankshaft and insert liners with holes and grooves for supplying oil into them so that the guide lugs sit in the grooves provided for them in the bearing seats. Copiously lubricate the liners;
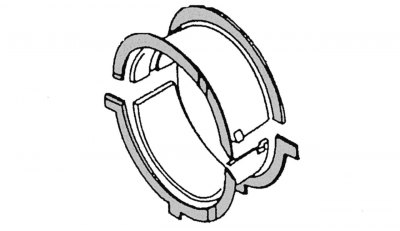
Pic. 81. Installation of semi-rings that regulate the axial clearance of the crankshaft
- on the corresponding main bearing, install adjusting semi-rings that regulate the axial clearance of the crankshaft.
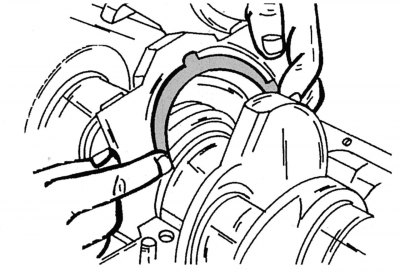
Pic. 82. Installing the main bearing cap together with the thrust semi-ring for adjusting the axial clearance of the crankshaft
These semi-rings with projections, based on the seat of the cylinder block and the main bearing cap, are exactly the same, so they should be installed as shown in fig. 81. The protrusions on the semi-rings serve to fix them from turning. The lubrication grooves must be directed towards the crankshaft flange, as shown in Fig. 82.
- Carefully lower the crankshaft into the bearing housings with shells. If the connecting rods with pistons were not removed from the cylinder block, put the bases of the connecting rods with liners on the connecting rod journals of the crankshaft;
- place the lower shells in the main bearing caps and generously lubricate their working surfaces;
- Place the thrust washers for adjusting the crankshaft axial clearance into the grooves of the middle main bearing cap. Oil grooves must be on the outside (see fig. 82). Holding the half rings on the right and left sides with your fingers to prevent them from falling out, install the cover on the corresponding main bearing pedestal;
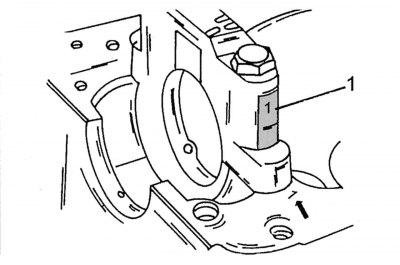
Pic. 83. Marking (1) main bearing caps
- install the remaining main bearing caps into their seats in the crankcase and tap them from above with a rubber or plastic mallet. Bearing caps must be installed taking into account their digital marking. For example: a unit stamped on the crankcase next to the bearing frame indicates that a bearing cap with a number marking should be installed on this bearing frame «1» (pic. 83). Thus, the numbers stamped next to the crankshaft main bearing posts must match the numbers on the bearing caps;
- tightening the bolts of the main bearing caps should be carried out in several stages, starting from the middle of the crankshaft and moving to its edges, finally tighten with a torque of 55 Nm. After that, in the same way, finally tighten these bolts by another 90–100°;
- rotate the crankshaft several times to identify possible jamming points;
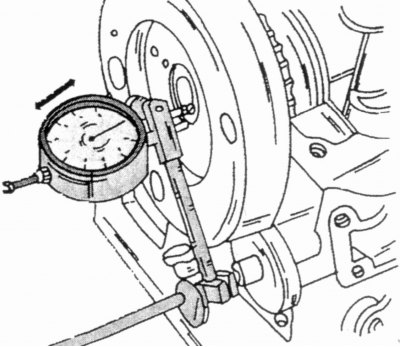
Pic. 73. Checking the axial clearance of the crankshaft
- once again check the axial clearance of the crankshaft according to the method described in subsection. «Removing the crankshaft», referring to Fig. 73;
- install pistons with connecting rods, taking into account the instructions contained in subsection 2.6.6;
- install the cover of the rear cuff of the crankshaft;
- install the camshaft drive mechanism (subsection 2.12.2);
- install flywheel (subsection 2.8.4);
- fasten the clutch to the flywheel, taking into account the markings. The driven disk must be centered;
- install oil pump (see the relevant subsection.).
Perform all remaining work in the reverse order of removal until the engine is fully assembled and ready for installation on the vehicle.