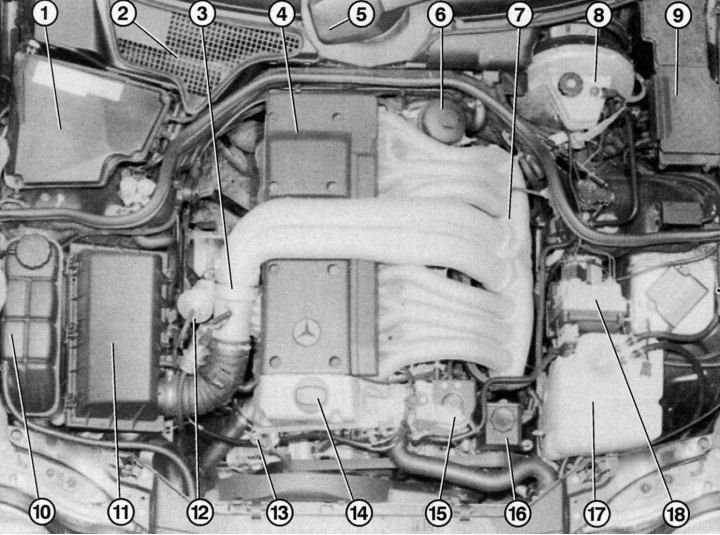
Pic. 4.5. Engine compartment with diesel engine 300 D: 1 - cooled plastic box for electronic controllers and relay blocks; 2 - grille of the air intake for ventilation of the passenger compartment; 3 - housing of pressure control valves; 4 – a cover of branch of atomizers and spark plugs; 5 - wiper drive; 6 - oil filter; 7 - intake manifold; 8 – reservoir for brake fluid with the main brake cylinder and brake booster; 9 - block of fuses and relays; 10 - expansion tank; 11 - air filter; 12 - bypass valve of the exhaust system; 13 - oil dipstick; 14 - oil filler cap; 15 - gasoline filter; 16 - spare capacity of hydraulic oil for servo control; 17 - washer reservoir (front - for headlights, rear - for windshield wiper); 18 - brake block
In addition to the 5-cylinder turbo engines, Mercedes offers a 3-liter 6-cylinder diesel engine (OM 606) (pic. 4.5). Technically, OM 606 almost completely corresponds to models OM 604 and OM 605 with a smaller number of cylinders (2.5 l, 5 cyl.). It is equipped with a cylinder head with a prechamber and four valves per cylinder, electronically controlled, in-line injection pump, dual-mass flywheel (models with manual transmission). The crankshaft of the 6-cylinder engine is mounted on seven support bearings. An exclusive feature of the OM 606 is the length-adjustable intake manifold in the form of a three-stage resonant intake manifold with dampers.
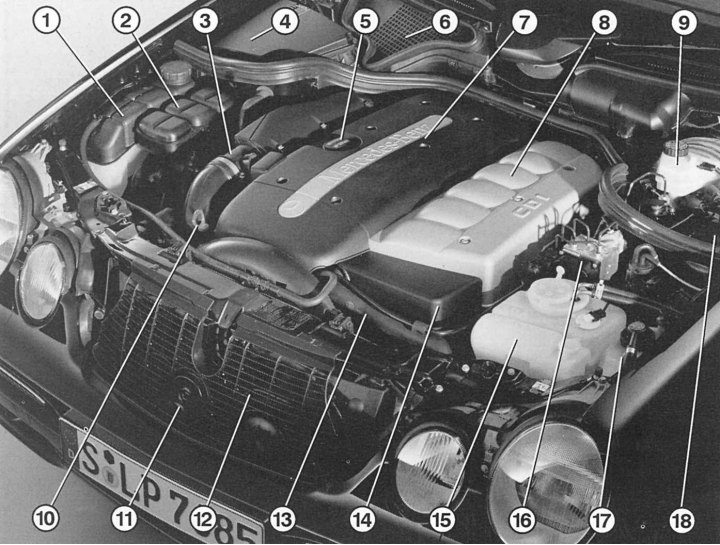
Pic. 4.6. Engine compartment with 320 CDI diesel engine: 1 - expansion tank; 2 - air filter; 3 – turbocharger air supply channel; 4 - cooled box for electronic regulators and relay blocks; 5 - oil filler cap; 6 - grille of the air intake for ventilation of the passenger compartment; 7 - engine cover; 8 - intake manifold cover; 9 – reservoir for brake fluid with the main brake cylinder and brake booster; 10 - oil dipstick; 11 - sound signal; 12 - protective grille; 13 - radiator hose; 14 – a cover of the petrol filter; 15 - washer reservoir (front - for headlights, rear - for windshield wiper); 16 - brake system control unit; 17 - spare capacity of hydraulic oil with a servo regulator; 18 - fuse box and relay
Since August 1999, the 320 CDI engine has been installed on Mercedes cars (pic. 4.6) with the Common Rail system, replacing the E 300 D.
All CDI engines are made in a modular system, they have the same distance between the cylinders (97 mm) and the same diameters and stroke (88 x 88.34mm). At the same time, CDI engines received a new cylinder head with four valves, centrally located injectors and aluminum construction.
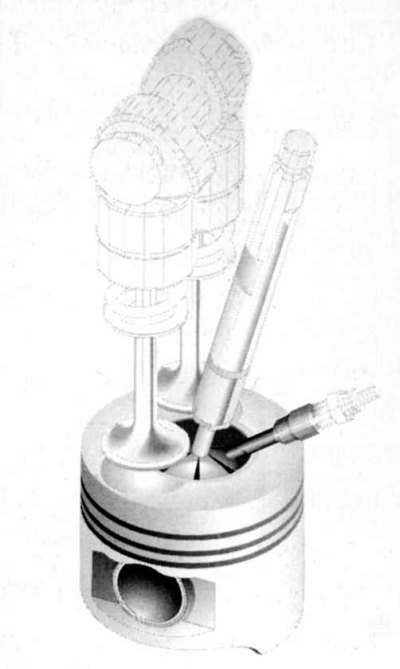
Pic. 4.7. Distribution of fuel in the combustion chamber
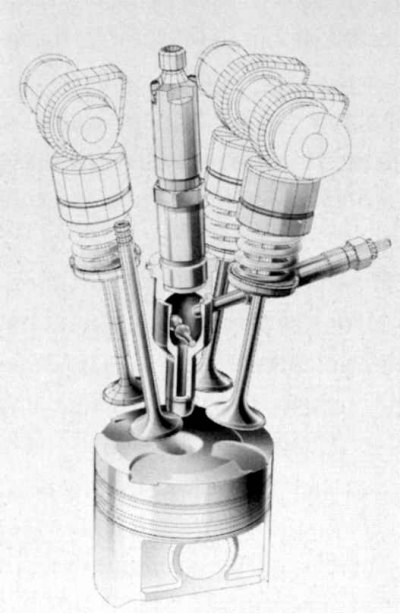
Pic. 4.8. Multi-valve system
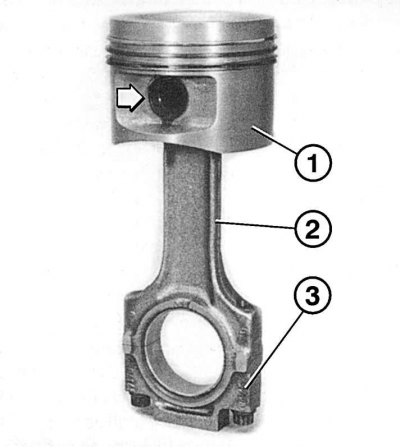
Pic. 4.9. Piston with connecting rod: 1 - piston with three piston rings; 2 - connecting rod; 3 – a cover of the basic bearing
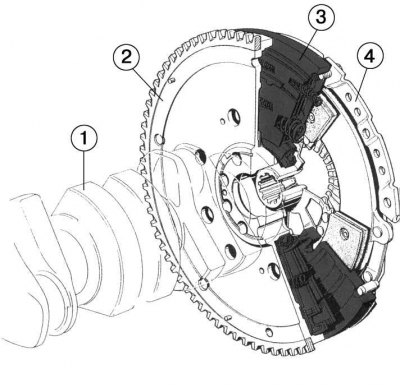
Pic. 4.10. Dual mass flywheel: 1 - crankshaft; 2 – a forward part of a flywheel; 3 – torsional vibration damper; 4 – a back part of a flywheel
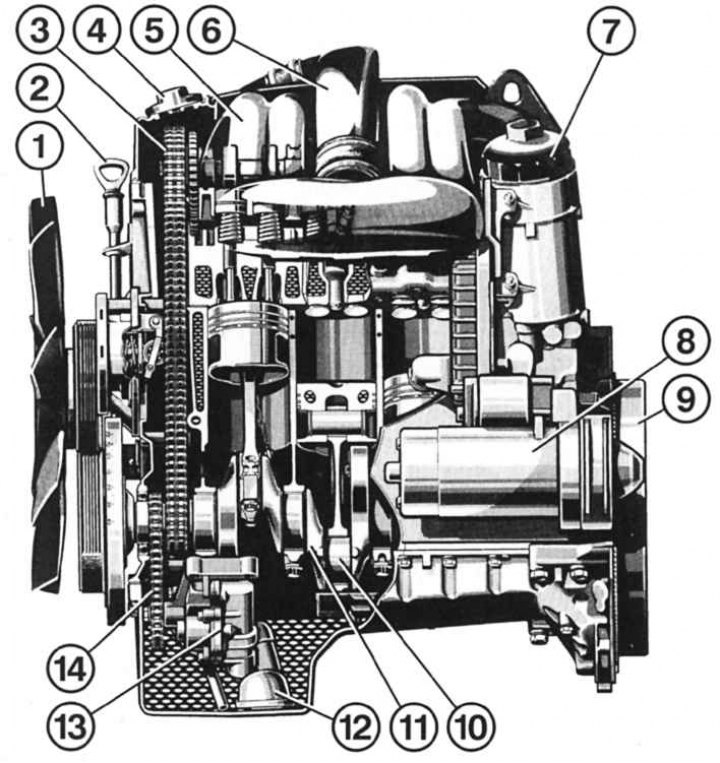
Pic. 4.11. Longitudinal section of a 4-cylinder diesel engine with prechamber injection (OM 604): 1 – fan with viscous coupling; 2 - oil dipstick; 3 – a chain of a drive of camshafts; 4 - oil filler neck; 5 - intake manifold; 6 - branch pipe from the control valve body; 7 - oil filter; 8 - starter; 9 - dual-mass flywheel; 10 - connecting rod with piston; 11 - crankshaft; 12 – receiving funnel of the oil pump; 13 - oil pump; 14 - oil pump drive chain
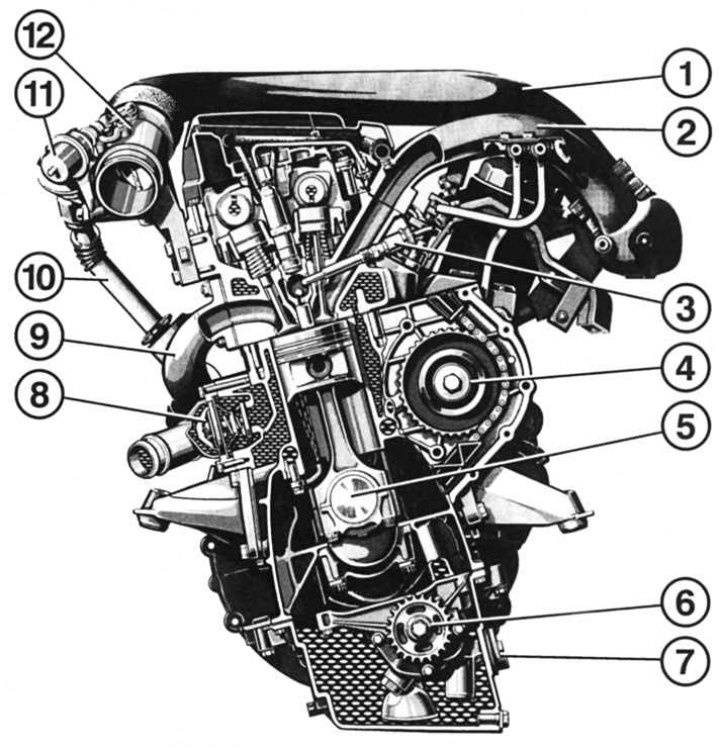
Pic. 4.12. Cross section of a 4-cylinder diesel engine with prechamber injection (OM 604): 1 - intake manifold of the intake system; 2 - intake manifold; 3 - glow plugs; 4 - gear wheel of the high-pressure fuel pump drive; 5 - connecting rod shafts of the crankshaft; 6 - oil pump drive gear; 7 - oil level sensor; 8 - thermostat of the cooling system; 9 - outlet pipe; 10 - exhaust gas recirculation channel; 11 - exhaust gas recirculation valve; 12 - control valve body
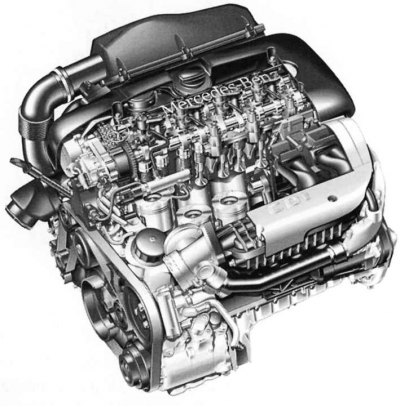
Pic. 4.13. Five-cylinder CDI diesel engine (OM 612)
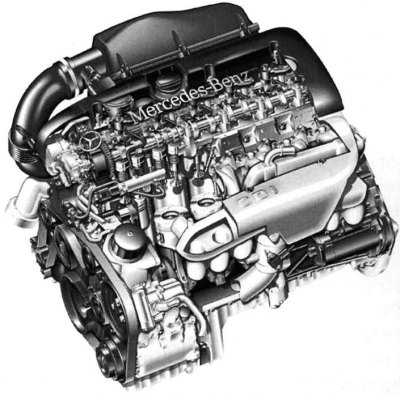
Pic. 4.14. Six-cylinder CDI diesel engine (OM 613)
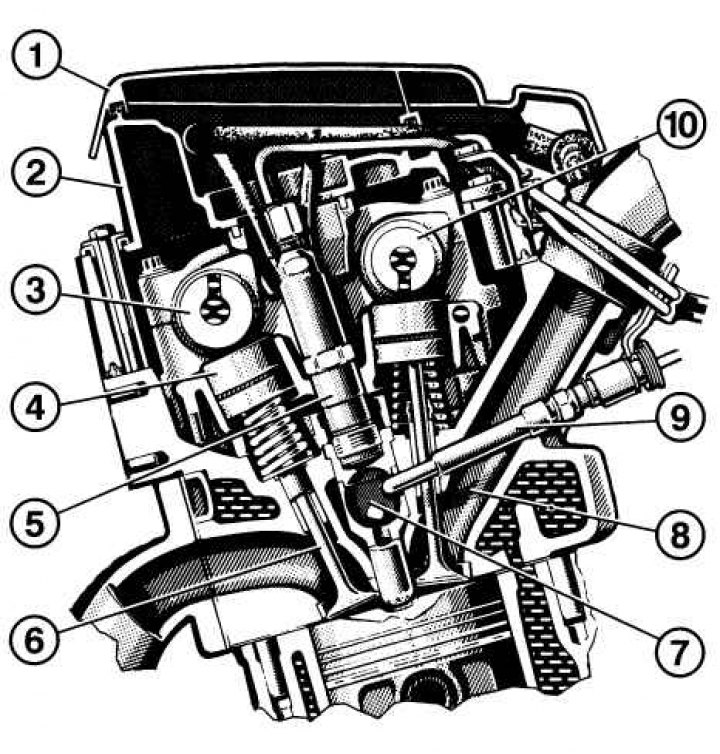
Pic. 4.15. The joint work of the camshaft and valves: 1 – a cover of a head of cylinders; 2 – a casing of a head of cylinders; 3 – a camshaft of final valves; 4 - pushers with hydraulic clearance adjustment; 5 - injection nozzle; 6 - exhaust valve; 7 - prechamber with an inlet channel to the combustion chamber; 8 - inlet channel; 9 - nozzle; 10 - intake camshaft
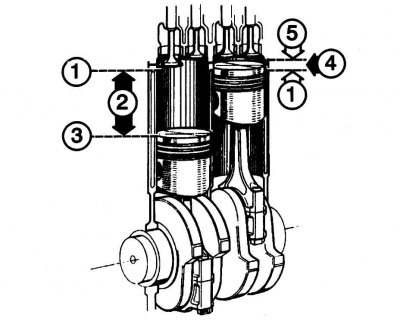
Pic. 4.16. Piston positions: 1 - top dead center; 2 - working stroke; 3 - bottom dead center; 4 - combustion chamber; 5 – a head of the block of cylinders
Multi-valve system
Four valve cylinder head. Engine power depends not only on the volume of cylinders and the number of revolutions, but also on the rate of entry of the air-fuel mixture into the combustion chamber and the rate of exhaust gases. Therefore, compared to a 2-valve system, a 4-valve system contributes to a more intensive filling of the combustion chamber (pic. 4.7). In addition, four smaller diameter valves have a much larger opening area than two larger ones (pic. 4.8). Combustion of fuel in engines with a 4-valve system occurs «softer», than in 2-valve engines, as there is less valve inertia. This helps to reduce the noise level during operation.
Engine parts
Cylinder block. In this largest and heaviest node is the crank mechanism. The cylinder block is made of gray cast iron. Inside the block are channels for water cooling. At the bottom of the block are pillows for the crankshaft support bearings. Blocks for the new 5- and 6-cylinder CDI engines are made of gray cast iron. Due to increased mechanical stress (direct injection) blocks have additional stiffening ribs and thicker walls.
Cylinder head. Closes the block from above. Made from light alloy. Compared to a gray cast iron head, it is more likely to warp due to insufficient cooling, improper installation or removal of a cold engine, but it is lighter in weight and has a higher heat transfer to the cooling system. The block head has channels for cooling, lubrication, intake system and exhaust system. It also has seats for glow plugs, injectors, valves and tappets. The camshafts are located on top of the cylinder head. Branch pipes are mounted outside on a head of cylinders. On the left are various sensors, switches and valves. The valve seats are made of hard metal. The aluminum cylinder head for the CDI models is characterized, among other things, by the presence of two helical intake ducts. One of them is used for swirling, the other for filling. Both channels correspond to the symmetrically made combustion chambers and serve for a strong swirl of air in front of the cylinders, which helps to create an optimal mixture of fuel and forced air. For uniform distribution of fuel inside the combustion chambers, new design nozzles are used, located in the middle of the cylinders.
Cylinders. The cylinders are integrated into the block and, together with the combustion chambers of the cylinder heads, form the volume of the cylinders. The inner walls of the cylinders are honed by the so-called mesh grinding method. Cylinder diameters are 0.02 mm larger than the corresponding pistons. When overhauling an engine, the cylinders can be reground up to 3 additional times, providing the appropriate repair size.
Pistons. They take on the pressure of the burning mixture and transfer the force to the crankshaft through the connecting rod. Made from light metal. The piston rings are located in the upper third of the piston. Top two rings (compression) prevent the penetration of gases during operation into the crankcase. lower (oil scraper) The ring removes oil from the cylinder walls.
Connecting rods. Connect pistons to crankshaft (pic. 4.9). The connecting rod head with a bronze bearing is connected to the piston by means of a loose pin. The connecting rod base is secured with a thrust bearing cap to the crankshaft.
Crankshaft. Converts the reciprocating motion of the pistons into rotational. To avoid vibration during operation, the shaft knees have counterweights. To prevent uncontrolled vibrations or deflection during operation, the bearing journals of the shaft are mounted with bearings on the engine block. Behind (in the direction of travel) at the end of the crankshaft, a support ring with a gear rim is installed to eliminate axial runout of the shaft. At the front end of the crankshaft are mounted gears for driving the camshaft and oil pump, as well as a pulley for the accessory drive belt.
Dual mass flywheel. Vehicles with a manual transmission have a dual-mass flywheel (pic. 4.10). It smooths out the torsional vibrations of the crankshaft that occur during engine operation. The front part of the flywheel is bolted tightly to the crankshaft 1. It has a torsional vibration damper 3, consisting of a system of springs and dampers. The rear of the flywheel is mounted on a vibration damper and is not rigidly connected to the front and crankshaft.
The appearance, sections and details of the engines are shown in fig. 4.11, fig. 4.12, fig. 4.13, fig. 4.14.
Valves. Through them, the injection of a combustible mixture and the release of exhaust gases are carried out.
Camshaft. With four valves per cylinder, both camshafts are mounted in a special housing.
The camshaft is used to drive the valves in a certain order. The moment of closing and opening is set by setting the crankshaft to a certain position (pic. 4.15).
The camshafts are driven by a chain from the crankshaft. Both camshafts have a gear mesh with each other. The gear on the camshaft has twice as many teeth as the gear on the crankshaft. According to the number of cylinders, the camshafts have different lengths. To save weight, the shafts are hollow.
Basic concepts about the operation of engines
Four-stroke principle of operation.
Inlet (1st measure): piston goes down to bottom dead center; The inlet valve opens and pressurized air enters the cylinder.
Compression (2nd measure): the piston goes from the bottom dead center to the top; intake valve closed; The pressure of the piston compresses the air.
Combustion (3rd measure): the compression temperature ignites the fuel, the fuel mixture during combustion pushes the piston to bottom dead center, and the connecting rod turns the crankshaft.
Release (4th measure): the piston goes up again, the exhaust valve is open, and the exhaust gases go into the exhaust system.
The working volume of the cylinder. The volume of the cylinder at which the piston passes from bottom dead center to top dead center is called the displacement. When the piston reaches top dead center, there is still a small amount of space left in the combustion chamber. The combustion chamber and working volume are shown in fig. 4.16.
Compression ratio. This is a characteristic of the relationship between the working volume of the cylinder and the volume of the combustion chamber. It shows how many times the combustible mixture is compacted before ignition.
Attention! Repair of components and parts on engines requires high qualifications and special tools. All work must be carried out exclusively at specialized service stations.